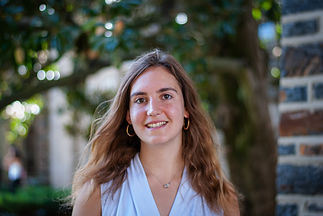
Innovation and Entrepreneurship Certificate
Look through to learn about my journey as an Innovation and Entrepreneurship student at Duke University.
Experiences
Damage Reducing
End of Arm Tool
Amazon Robotics
Summer 2022
Hardware Design Engineering Intern
As part of the Sparrow team that was tasked with manipulating prepackaged items in crowded totes and isolating them for future sortation, I worked specifically on the end effector in order to reduce damages and develop a better testing method for future end effector comparisons. An overview of the Sparrow robot and its corresponding end effector Daisy can be seen below.
While the video highlights many of the cool features of Sparrow including multi-modal sensing and advanced perception I was specifically tasked with the hardware design of Daisy, the end effector. While super effective at picking some objects there were certain objects where damage was super common such as book covers, shoeboxes, mesh objects, shrink wrap, or things with pointy and unique shapes. However it was initially really hard to understand the pros and cons of each manipulation method because each test was run in a different environment (tote vs isolated vs crowded) using different test sets. It was through the first weeks of onboarding that I learned the importance of developing good tests and standardizing control variables during testing.
This inspired be to spend the first half of my internship going through the data on other end effectors in development to really understand exactly where Daisy was failing and if any other end effectors were able to solve that problem. As such a developed a new standardized test set and procedure, that was reusable and repeatable something that didn't exist before I started. There were two main tests - a Daisy current damage test set as well as an overall representation of the objects that a typical robot could expect to see (even though it varies greatly by time of year and location). This work then let into the design of a new hybrid end effector that build off Daisy's success, while not damaging even more of the objects.
​
One of the biggest challenges I encountered in this role was designing for scale. Having never worked on such a big project, I usually deprioritized cycle life and repeatability in my designs however when working on this team, I was not just thinking about parts per million but wanted to ensure that the end effector would be able to last multiple million picks per day for over 6 months. My new design combined a central toroidal gripper with 6 suction arranged similar to Daisy. This allowed the software to choose between manipulation methods depending on the circumstance and reduced damages by 60% according to my testing procedure. However the flexible membrane of the toroidal gripper was very susceptible to being punctured and stress over so many cycles which would need to be tested further before being deployed into fulfillment centers.
​
6 months after my internship Daisy was deployed over other end effectors in development. While a lot of the design is kept confidential and a lot of the internal testing is not available publicly, the video below, an artifact from my internship shows Daisy undergoing one of the tests. Also attached is the Amazon Manipulation Picking Dataset - using some of the data I collected and releasing it publicly to encourage research and development with these challenging manipulation challenges.
Directed Energy Thermolysis
Focused on using Directed Energy for military and more specifically counter UAS threats, I had never worked in a start up environment before. I quickly fell in love with the fast paced environment and the get it done mentality. The company had developed one MVP and were quickly working to make necessary improvements, build out more systems and see if their technology could be used for other purposes. One such idea that was give to me on my first day was to research and understand if the high amounts of power able to be generated while neutralizing drone threats could be turned and used to combat global warming by breaking down CO2. As such I spent the rest of my internship developing proof of concept, doing the necessary calculations to back up my predictions, leading design talks to the CEO, CTO and other executive members and eventually building an initial MVP.
​
While the team was super and supportive of me and definitely willing to answer any questions that I had during the process, there was always a lot of doubt around my ideas because there was not anyone who had done it before. I remember walking into my first design review and after talking for 10 minutes one of the engineers interrupted me and said "So you are basically building a bomb" (I was not) because he doubted the ability for the process to work. After running him through all of my calculations and research by the end of the meeting he was supportive of me building an initial MVP in the parking lot behind the office. This taught me the importance of being able to defend your design decisions and being able to communicate effectively and efficiently.
​
One of the biggest challenges I faced was finding resources to help inform my thinking and back up my idea, especially because there was no research that had been done on this specific idea. I quickly learned that while an exact solution might not exist there was lots of resources available for decomposing each part such as breaking down CO2 and lots of people at the company to talk to about the power generated from L-Bands.
​
For my artifact, during the summer internship I was able to file a preliminary patent for my work on this project and a little less than a year later the company filed the full patent.
Marr, H.B., Bedingfield, M.B., Goehringer, A.I., Dower, W.G., Lee, J.J., Rau, L.G.,
Verstandig, G.L., “Systems and Methods for Decomposition of Molecules,” Unites States
Patent, No. 20230015528